Metal and stainless steel storage tanks often contain highly corrosive or caustic materials that degrade and break down their containers. Conducting regular aboveground tank inspections is incredibly important for detecting any potential storage tank failures that could be detrimental to facilities, personnel, and the environment. Inspections can help plant leaders catch red flags at the onset of problems before they become full blown disasters. So, how do inspectors know what exactly to look for?
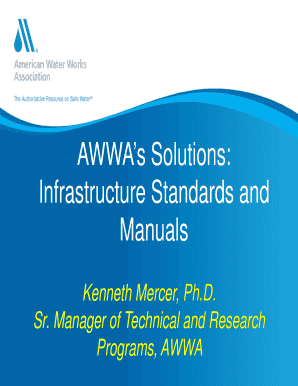
Tank inspection standards
Api 653 Standard Pdf Free Adobe Reader
- Free Api 653 Tank Standards.pdf - search pdf books free download Free eBook and manual for Business, Education,Finance, Inspirational, Novel, Religion, Social, Sports, Science, Technology, Holiday, Medical,Daily new PDF ebooks documents ready for download, All PDF documents are Free,The biggest database for Free books and documents search with fast results better than any online library eBooks.
- API 653 Inspector Certification Training Study Suggestions MSTS 4 January 2007 API 650 STUDYING INSTRUCTIONS - Don't read API 650 cover-to-cover. Remember API 650 is the fabrication code for new tanks. But API 653 often refers to API 650 during repairs and alterations. As you study API 653 and see a reference to API 650, go ahead.
- If any provision of API standard 653 presets a direct or implied conflict with any statutory regulation, the regulation will govern. In the event that API standard 653 provisions are more stringent than statutory regulations.
Today, many standards exist for inspectors to use as guidelines for identifying issues and determining what specifications facility leaders should meet upon tank inspections. The American Petroleum Institute (API) has established several key standards to help inspectors recognize risks. One such standard includes the API 653 standard, which “provides minimum requirements for maintaining the integrity of such tanks after they have been placed in service and addresses inspection, repair, alteration, relocation, and reconstruction.”
American Petroleum Institute (API) Standards 650, 653 and 620 are the primary industry standards by which most aboveground welded storage tanks are designed, constructed and maintained. These standards address both newly constructed and existing aboveground storage tanks used in the petroleum, petrochemical and chemical industries.
Tanks should only be inspected by a licensed, certified API 653 inspector. An API 653 inspector must have at least four years’ experience with storage tanks and pass a specialized test to prove his or her competency in the field. He or she should inspect various safety components, including tank location, materials and construction, spill control, and so forth. Tank inspections should also include tank integrity inspection aspects including roofs, shells, and bottom structures; corrosion analysis; and settlement evaluation. This type of inspection helps experts identify leaks into catchment containers or groundwater, determine and monitor corrosion rates, pinpoint maintenance and repair tasks and, most important, prevent large scale tank failures that pose real risks.
Api 653 Tank Inspection Standards
Inspections should occur at the following intervals:
- Tank operators should conduct internal inspections once every five years. In this case, the inspector is not required to be certified but simply knowledgeable enough to identify problems or potential problems.
- Certified API 653 inspectors should perform external inspections every five years based on regulatory requirements.
- Owners and facilitators must also have certified inspectors conduct internal API 653 inspections every 10 years.
It’s important to keep maintenance and inspections records on hand and up to date. Plant managers should also record any follow up actions they take to address hazards found during inspections.
Tank corrosion
Both internal and external inspectors should look at high risk areas where piping and metal containers are likely to corrode. Inspectors can look for corrosion along weld or sealant lines. Other areas of concern include piping corrosion, bottom and roof corrosion, as well as any other signs of leaks, failures, or weak points that can cause tank malfunctions. Over time, monthly inspectors should be able to determine the rate at which corrosion is taking place in storage tank systems. Depending on the holding materials and types of storage containers, corrosion rates will vary. Plant leaders can use these corrosion rates to better plan for future repairs and part replacements based on how long it will take their systems to eventually fail.
To calculate corrasion rates, include the following factors:
- Weight loss — the decrease in metal weight during the reference time period
- Density — density of the metal
- Area — total initial surface area of the metal piece
- Time — the length of the reference time period
To make the process easier, inspectors can use a corrosion rate calculator. However, remember that knowing your corrosion rates is not enough: You’ve also got to take action. Understand what causes corrosion and work to proactively avoid it. For instance, always use corrosion resistant linings to reduce maintenance costs and protect your facility’s viability.
The experts at Moon Fabricating Corporation are your partners in tank, ductwork, and piping repairs. As you begin to spot corrosion and other signs of tank failure, we will work with you to repair and replace stainless steel or other metal tanks to meet safety and regulatory requirements.We are dedicated to your success and safety; repair services are one of the ways we meet that commitment. Are your tanks in need of replacement, repair, or linings? Contact us! We’ll help you determine the safest and most cost effective route to keep your tanks in production.